How Doctors and Engineers Teamed Up to Produce a Hospital Coronavirus Face Shield — Fast
Short on the crucial protective gear, NewYork-Presbyterian joined forces with Columbia University engineers to design and manufacture its own face shields to protect healthcare workers from the coronavirus.
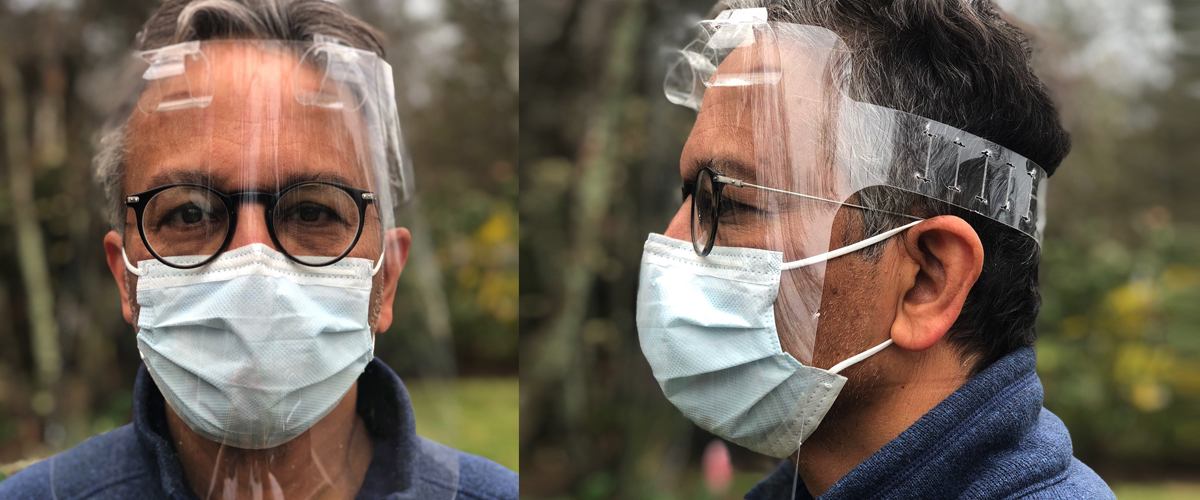
Dr. Anil Lalwani
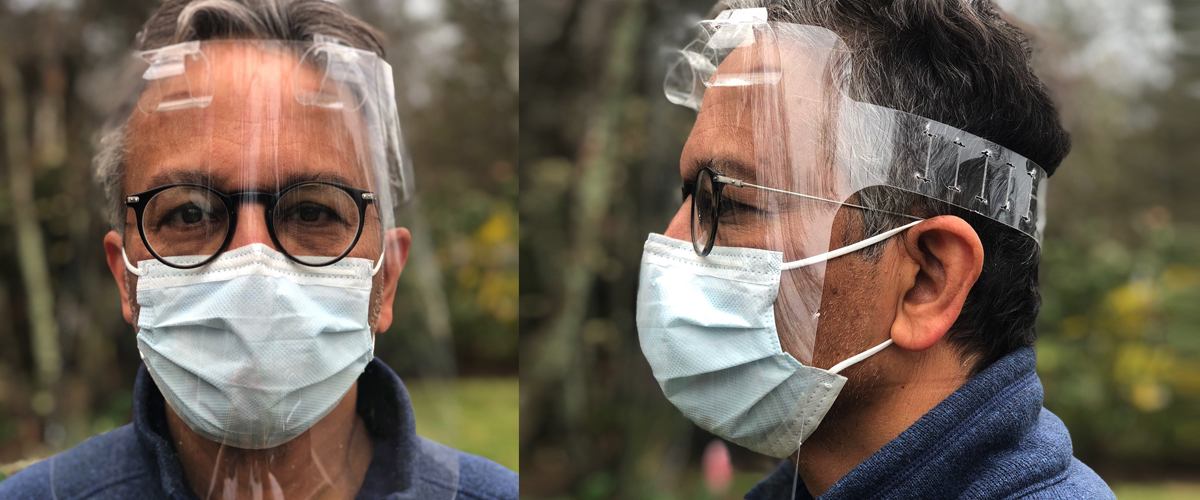
Dr. Anil Lalwani
Jeffrey Kysar received an urgent email from NewYork-Presbyterian one recent Thursday.
The hospital needed more face shields. As chair of the Department of Mechanical Engineering at Columbia University’s School of Engineering and Applied Science, could he find a way to fast-track the design and production of face shields for healthcare workers treating patients who might have the coronavirus?
“We were astonished that the need would escalate to about 50,000 per day,” says Kysar.
He put out a call. Nearly instantly, engineering school students, staff and faculty began holding virtual meetings to brainstorm and collaborate on designs. Soon, physicians from NewYork-Presbyterian and Columbia University Irving Medical Center joined the video calls, giving immediate feedback and suggestions.
“It was all hands on deck,” Kysar says. “I was absolutely bowled over by the response.”
Seventy-two hours later, NewYork-Presbyterian had approved a face shield prototype to begin testing with its healthcare workers. The engineering school, meanwhile, began churning out 1,000 shields a day in its new Makerspace until a larger batch arrived from the manufacturer. The field testing by medical staff was successful, and NewYork-Presbyterian has scaled up the mass production for deliveries of 50,000 per day.
“It’s the collaboration across medicine and engineering that made this happen,” says Dr. Anil Lalwani, who was part of the design process and is medical director of perioperative services at NewYork-Presbyterian/Columbia University Irving Medical Center, and vice chairman of otolaryngology – head & neck surgery and co-director of the cochlear implant program at Columbia University Vagelos College of Physicians and Surgeons. “Engineers are perfectionists. You wouldn’t believe how many millimeters they want to get perfectly right, and the surgeons just want to get it done. So it was a combination of precision and speed that made it possible to come together and execute this in real time.”
Like a cookie cutter
Healthcare workers wear the plastic shields over their face masks when they treat patients with possible or confirmed COVID-19, the disease caused by the coronavirus. The shields protect the workers from droplets, such as from coughs and sneezes, that can transmit the virus. NewYork-Presbyterian’s welder-style shield is disposable and covers the entire face from the forehead down. The design can be produced for less than a dollar and made in seconds.
Dr. Anand Joshi, vice president of procurement and strategic sourcing at NewYork-Presbyterian, told the design team that a key requirement was that “we have to be able to make a lot of these very quickly.”
The manufacturing plant, located in Connecticut, uses a process called die cutting, which is “literally no different than using a cookie cutter to cut out a shape of dough,” Kysar says. This industrial method is fast and can produce more than 50,000 face shields a day.
To speed up production, healthcare workers fold the flat piece of plastic themselves in several places to turn it into a wearable face shield.
“It’s extremely simple” for workers to assemble on the spot, Dr. Joshi says.
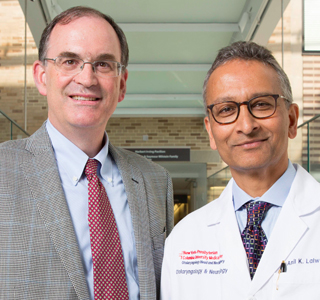
Jeffrey Kysar (left) and Dr. Anil Lalwani
One week’s time “is remarkable”
After Dr. Joshi asked the engineering school for help that Thursday, the team had designed several versions by the next day and turned them into prototypes, which they shared with NewYork-Presbyterian. That Saturday morning, mechanical engineering lecturer Yevgeniy Yesilevskiy took a deserted subway and hand-delivered a prototype to the home of Dr. Yoko Furuya, medical director of Infection Prevention & Control at NewYork-Presbyterian Hospital and associate professor of medicine in the Division of Infectious Diseases at Columbia University Irving Medical Center. She suggested a strip of foam on top for a more secure fit. Although face shields are typically two pieces, adding a second piece would slow down the manufacturing process; even a few extra seconds would delay mass production. Also, including foam in the design could delay the start of mass production by up to two weeks. The team got back to work, making adjustments but keeping it one piece.
“It’s wonderful to see engineers and doctors coming together, amid all the chaos and uncertainty, to protect healthcare workers on the front lines.”— Dr. Anil Lalwani
Saturday night, Yesilevskiy borrowed a car and drove the updated prototype to NewYork-Presbyterian/Weill Cornell Medical Center, where Dr. David Calfee stood outside waiting for the handoff. Dr. Calfee, deputy medical director of Infection Prevention & Control at NewYork-Presbyterian Hospital and professor of medicine in the Division of Infectious Diseases at Weill Cornell Medicine, shared it with intensive care unit physicians who wore it that night. Late that night, Drs. Calfee and Furuya gave the green light.
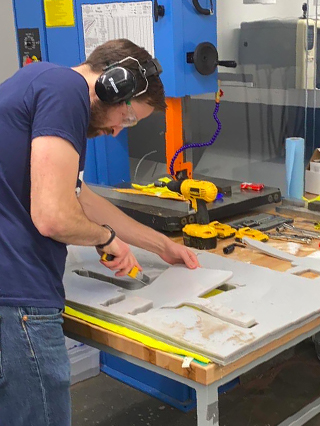
Yevgeniy Yesilevskiy preparing the face shields for packing in the Makerspace at Columbia University’s Engineering School.
The Columbia designers called around to almost every plastic distributor in and near New York City to find precut sheets of plastic so they could start cutting out the face shields themselves until the manufacturer was ramped up. That Sunday night, the first plastic shipment arrived. Yesilevskiy and two co-designers unloaded it off the truck, hauled it upstairs, and began stacking the sheets in a water jet cutter, a machine so new that they were learning on the fly how to use it. They stayed up all night churning out face shields. “My Fitbit counted that I was on my feet for 23 miles that day,” Yesilevskiy says.
Soon, the design team delivered 200 face shields for clinicians to test, while the Makerspace began producing 1,000 a day. One week after Yesilevskiy hand-delivered the prototype to the two doctors at NewYork-Presbyterian, the manufacturer delivered 8,250 face shields so that workers could try the industrial version. Responding to feedback from healthcare workers, the design team tweaked it again recently, shortening the shield’s length. NewYork-Presbyterian has scaled up its deliveries to 50,000 a day. With the COVID-19 outbreak hitting its apex, the face shields have been as critical as ever.
“University innovations usually take years or even a decade to make an impact on patients. To make such a positive impact in one week’s time is really remarkable,” says Orin Herskowitz, executive director of Columbia Technology Ventures and senior vice president of intellectual property and tech transfer at Columbia University. “This and other face shield designs from Columbia’s engineering team are now in use or production at other New York City hospitals, as well as in Europe, Thailand, and around the globe.”
“The face shield with a simple, elegant, and highly functional design has worked effectively in protecting our healthcare workers from COVID-19,” adds Dr. Lalwani. “As a member of the medical center family, it’s wonderful to see engineers and doctors coming together, amid all the chaos and uncertainty, to protect healthcare workers on the front lines.”
Additional Resources
Learn how to protect yourself during the coronavirus outbreak and what to do if you think you’ve been exposed.
Telemedicine has become an essential tool as people are encouraged to stay home. Learn how to have a better virtual visit. If you are not feeling well, consider using NewYork-Presbyterian’s Virtual Urgent Care for non-life-threatening symptoms.